The Process of Creating Custom Made Inflatables: From Concept to Creation
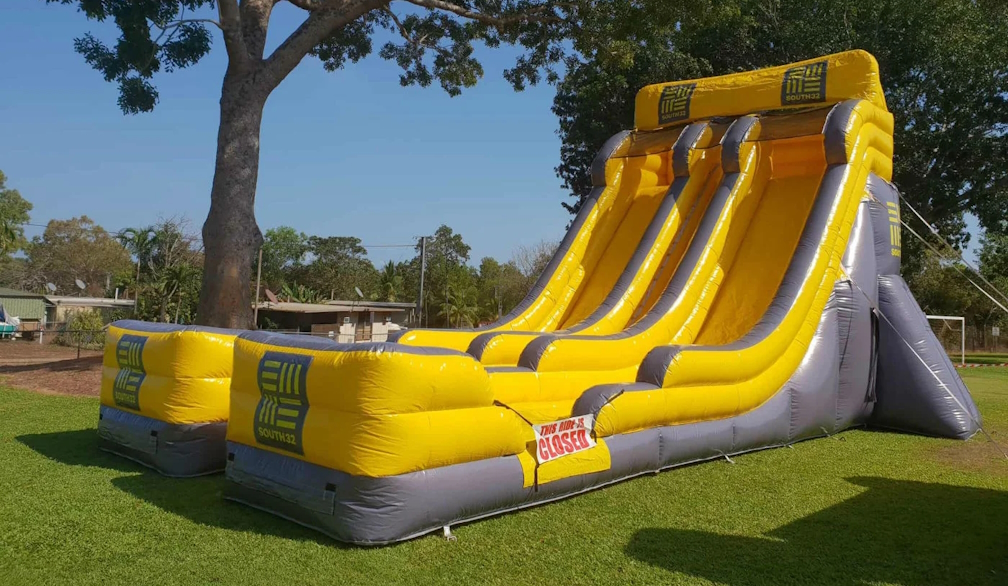
Custom-made inflatables are the kind of marketing tool that turns heads. Whether it’s a larger-than-life version of your product or a playful mascot floating above an event, these inflatables bring brands to life in a big way. But what’s involved in making these eye-catching creations? Let’s walk through the process, from the initial concept to the final inflatable masterpiece.
1. Concept Development: Bringing Your Vision to Life
Every great inflatable starts with an idea. This is the most crucial step, as it’s where your vision begins to take shape. Whether you’re thinking of a giant product replica, a whimsical character, or an interactive inflatable, the concept development phase is all about defining your goals and imagining how the inflatable will look and function.
During this phase, you’ll work closely with a team of designers and engineers who will take your ideas and transform them into a viable design. Consider the following questions:
-
- What purpose will the inflatable serve? Is it for branding, entertainment, or something else?
-
- Where will it be used? Indoors, outdoors, or at a specific event?
-
- How big should it be? Do you want something massive that dominates the space or something more subtle?
Once the concept is clear, designers create sketches and 3D models to visualize the inflatable. This helps you see how the final product will look and allows for adjustments before moving forward.
2. Design and Engineering: Crafting the Details
Once the concept is locked in, it’s time to get into the nitty-gritty of design and engineering. This step involves translating the sketches and models into detailed technical drawings that will guide the manufacturing process. During this stage, every aspect of the inflatable is meticulously planned out—from its dimensions to the materials that will be used.
The design process takes into account factors such as durability, portability, and safety. Depending on your needs, the inflatable can be designed to withstand different environmental conditions, like outdoor events or prolonged exposure to sunlight. Engineers also consider how the inflatable will be inflated, anchored, and maintained during its use.
Color selection, branding elements, and finishing touches are also finalized in this stage. Whether it’s bold colors to grab attention or precise logos to represent your brand, every detail is carefully crafted to ensure the inflatable aligns with your vision.
3. Prototyping: Testing the Design
Before the full inflatable is created, a prototype may be produced. This is a smaller or simpler version of the final design used to test the materials, construction, and overall design. Prototyping is an important step because it allows you to see the inflatable in action and make any necessary adjustments before committing to the full-scale production.
During this phase, the team checks for issues such as balance, inflation time, and visual impact. Any changes that need to be made—whether it’s tweaking the design for better stability or adjusting the colors—are handled before moving on to the final manufacturing stage.
4. Manufacturing: Bringing the Inflatable to Life
Once everything has been approved, it’s time to bring the inflatable to life! During manufacturing, skilled technicians use specialized equipment to cut and sew the materials based on the technical drawings. Depending on the complexity of the design, this can involve multiple layers of fabric, reinforced seams, and intricate detailing.
Manufacturing is a blend of craftsmanship and technology. While automated machines handle precise cutting and sewing, experienced workers oversee the assembly, ensuring that every detail is perfect. After the inflatable is assembled, it goes through a series of quality checks to ensure that it meets safety standards and matches the original design.
5. Inflation and Testing: Ensuring Perfection
Once the manufacturing process is complete, the inflatable is tested to ensure that it works as intended. This involves inflating it to its full size, checking for any leaks, and making sure it stands up to real-world conditions. This is the final opportunity to make any adjustments before the inflatable is shipped out.
During testing, technicians will also inspect how the inflatable inflates and deflates, how it holds its shape, and how it responds to wind or other environmental factors. If everything checks out, the inflatable is ready to be packaged and sent to you for use at your event or installation.
6. Delivery and Setup: Show Time!
Finally, your custom inflatable is ready for delivery. Depending on the size and complexity, the inflatable may arrive in one piece or in sections that need to be assembled on-site. Inflatables are designed to be easy to set up and take down, so you can get them ready for your event with minimal hassle.
Many manufacturers provide detailed instructions or even on-site assistance to ensure that your inflatable is set up correctly. Once it’s in place and fully inflated, your inflatable is ready to make a splash at your event!
In Summary
Creating a custom-made inflatable is a fascinating process that combines creativity, engineering, and craftsmanship. From the initial concept to the final product, every step is designed to bring your vision to life in a fun, impactful way. Whether you’re looking to promote your brand, entertain guests, or create a memorable experience, custom inflatables offer endless possibilities to make a lasting impression.