Tips For Planning A Successful Knockdown Rebuild In Sydney
- Written by NewsServices.com
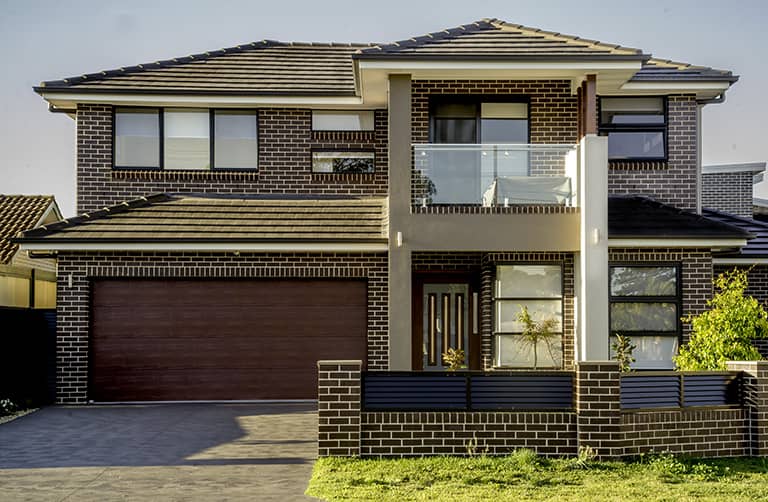
If you love the place you live in, but your current house is no more according to your requirement, a knockdown rebuild is an option that will suit your needs perfectly. With this option, you can easily get your dream house built in your beloved neighbourhood on the land you already own.
What Is A Knockdown Rebuild?
Knockdown rebuild or KDR means to bulldoze your current home and get a brand new house built in the same place as before. However, the new house built over the land is more accommodating and according to your needs.
This way, you won't have to leave behind the friendly neighbours and area you love.
Process Of A Knockdown Rebuild
The process of a knockdown rebuild Sydney is more straightforward than buying a house. Let us briefly take a look at its process;
- * Select a design for your new house. You can get your home designed by designers, or you can also design the house yourself.
- * After finalising your dream house design, you need to get it approved by the council. You can ask your contractor to do that for you.
- * After approval, you need to get your home inspected by the builder so that you can discuss the limitations that might arise during construction and their solutions.
- Finally, it is time for you to sign the agreement and start the procedure of knockdown rebuild.
Top Things People Should Know While Planning the KDR
Knockdown rebuild in Sydney is rapidly gaining popularity. It is one of the most accessible house-building ideas in the market. If you are thinking about going for this option, you should remember the following factors while planning KDR.
- * Chose the piece of land you want to build a house on. Most people prefer the area they live in. but, you are also free to select another piece of land.
- * Plan the house according to your budget. Rebuilding a home is not as expensive as renovating or buying a new house. You will be surprised to see that the price of tearing down the house and getting a new one is less than other housing options. But, you will be in more advantage if you plan a budget. Get an estimation from the builder and then plan a budget around it.
- * Save yourself from unnecessary problems. You need to follow all the rules and regulations of the area you live in. since you are practically building a new house, you need to take care of neighbourhood properties, council controls, land issues, and legal rights.
- * Find a temporary space to live until your house is being rebuilt. You will need to add the cost of temporary living space to your budget. The whole process can take up to a year to complete, so find accommodation accordingly.
Benefits Of Choosing Knockdown Rebuild Sydney
There are many benefits of choosing knockdown rebuild in the long run, but the most prominent is that once you select this process, you will have control over what you get built and the flexibility of a unique house design. Apart from this, the Sydney knockdown rebuild is also a cost-effective option.