What is the importance of occupational health and safety in construction industry?
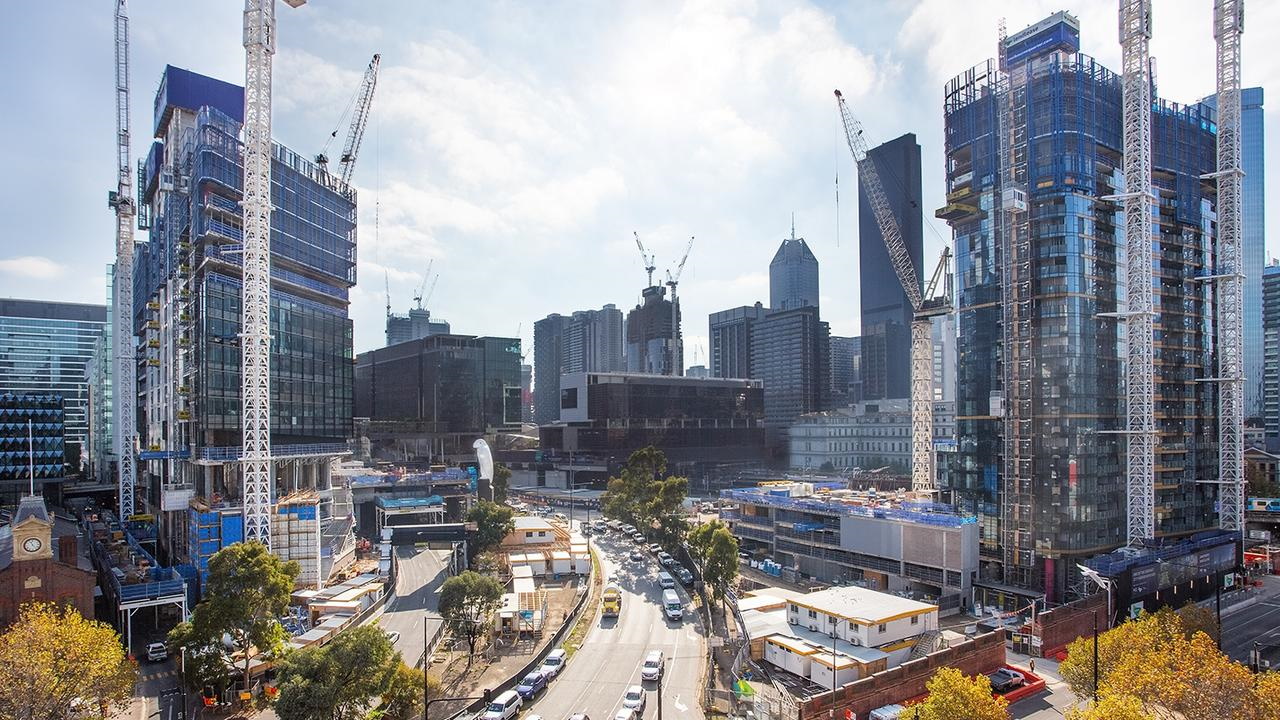
Work health and safety (WHS) also known as Occupational Health and Safety (OH&S), refers to the laws, policies, and programs involved in the management of health and safety risks of an organisation’s employees, clients, suppliers, and all other stakeholders. It goes without saying that WHS is a major concern for all organisations, but that concern is further heightened for those working in high-risk industries, such as the construction industry, where heavy machinery, hazardous material, electricity and moving objects regularly interact with each other, making construction sites one of the most dangerous workplace in the world.
Why should we have occupational health and safety in the workplace
Every year, thousands of construction workers are injured on the job and hundreds lose their lives. According to Safe Work Australia, in 2020, the construction industry accounted for over 14% of overall work-related fatalities. In this article, we discuss the importance of WHS in construction,iso 45001 certification cost ,and share our top 3 reasons why worker safety should be the number one priority of every
construction organisation worthy of the name.
1. Importance of whs for stakeholders
Research shows that injuries and fatalities typically occur when workers are struck by a moving object, fall from a height, or are involved in an accident with a vehicle or heavy machinery. Although it is impossible to entirely eliminate risk, having effective health and safety measures in place can reduce it substantially.
Should we have occupational health and safety in the workplace?
Construction industry workers are also prone to various industry specific illnesses, resulting from being exposed to toxic material, or the prolonged use of certain tools and equipment. Job conditions in the industry are also known to be contributing factors for poor mental health. Each year, 190 construction industry workers in Australia take their own lives. So having and benefits of ISO 45001 became a little clearer, right? There are many hazards to be aware of in all workplaces. Be particularly careful with large handling equipment. Visit All Star Access Hire & Scaffold for boom lift hire.
The likelihood of workers committing suicide in this industry to is twice as high as is it for the rest of the country. Construction organisations are not only responsible for the safety of their workers, they are also responsible for the Safety of all stakeholders. These include members of the public, visitors, sub-contractors, suppliers, and anyone else who might be exposed to hazardous situations or material on or near your construction site.
2. Is occupational health and safety a legal in australia?
In Australia, any organisation carrying out construction work, is legally required to ensure WHS risks are properly managed and controlled. Construction organisations are also legally obligated to secure their construction sites and prevent any unauthorised access. Australia has one of the strictest codes for construction in the world and head contractors are required by law to be aware of and in compliance with all applicable WHS duties. The Model Code of Practice for Construction work provides practical guidance to assist duty holders achieve compliance with WHS Act, duties, and regulations.
Under the Australian WHS Act, all workers must complete general construction induction training before they can carry out construction work. This safety training is also referred to as white card training. There are also various legally mandated licences associated with different types of high-risk activities such as cranes, hoists, and forklifts. Visit All Star Access Hire & Scaffold for boom lift hire.
Because of the alarming level of work-related serious injuries and fatalities Safe Work Australia has designated the construction industry as a priority in the Australian Work Health and Safety Strategy 2012–2022, with the aim of reducing the number of serious injury incidents in Australia by at least 30% and work-related fatalities by at least 20% by 2022.
3. Role of occupational health and safety to prevent failure in work
Failure to offer workers an effective WHS management system and ensure they understand WHS policies and procedures can lead to dire consequences for construction organisations. Without proper WHS processes in place, workers are more likely to get injured or become ill and miss work, which in turn lowers productivity and profitability of the project and overall organisation.
Failure to make the necessary WHS arrangements constitutes breaking the law and may lead to hefty fines or even imprisonment. Organisations may also have their authorisation to carry out construction work revoked, not to mention legal actions that can and will be brought against them by stakeholders victim of the consequences of their failure to follow WHS laws.
Because no buyer wants to work with an organisation with a bad history of injuries or fatalities, coming back from such reputational damage is extremely difficult, and organisations who find themselves in such situations go out of business, more often than not.
With WHS ISO protect your workers as well as the stakeholder
Although developing and implementing an effective WHS management system can prove to be a time-consuming and resource-draining process, it is absolutely necessary for construction organisations, to protect their workers and stakeholders, to ensure all regulatory and legal requirements are satisfied, and last but not least, so they can actually be profitable, enjoy a healthy reputation and have a fighting chance in this highly competitive industry. Construction organisations are advised to start this process early, so they can incorporate WHS measures into the fabric of their organisation and turn safety into a culture, instead of just a legal obligation.