Everything You Wanted To Know About Air Compressors
- Written by News Company
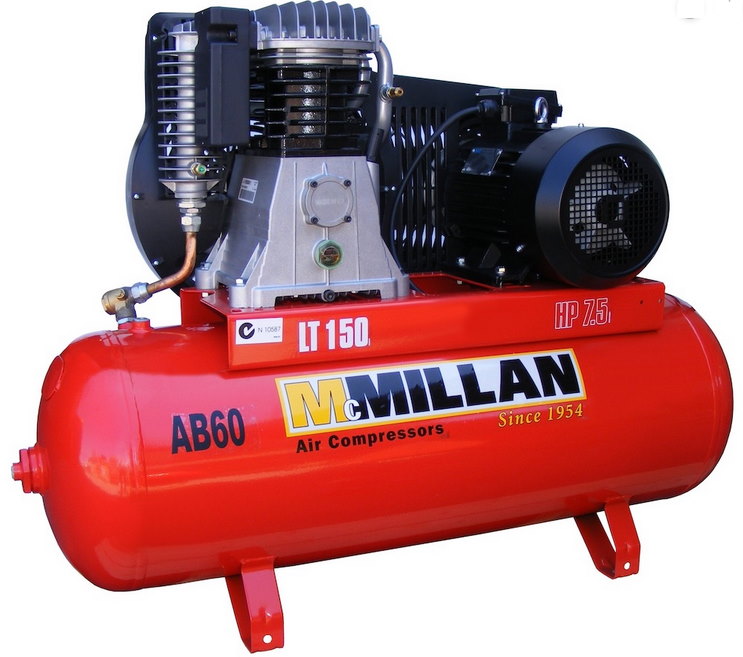
An air compressor can be described as a device that converts power into potential energy stored in compressed air. The air compressor is responsible for forcing more air into a storage tank, thereby increasing its pressure. According to the experts in the industry, air compressors are used to power a wide range of equipment, including paint sprayers, impact wrenches, and so on.
Different types of Air Compressors
Some compressors are designed using a rotating impeller to help generate air pressure. However, air compressors with a positive-displacement compressor are more popular these days and the air compressors work like a small combustion engine and it consists of a crankshaft, a cylinder, pistons, and a valve head. They also have an air tank to store a predetermined quality of air with a present pressure range. The energy of the pressurized air is ultimately used to drive air tools.
Typically, air compressors comprise one or two cylinders, depending on the tools they will have to power. Homeowners prefer to use a two-cylinder air compressor model that works like the single-cylinder model, except for the difference that there are two strokes during each revolution instead of just one.
Air compressors are fitted with a pressure switch to allow you to stop the motor when the pressure in the air tank reaches the preset limit. It is usually around 125 psi in most single-cylinder models. The compressors also come with a safety valve in case of a malfunction.
The piston compressors are well lubricated by the oil bath. The oil bath is responsible for making sure that the cylinder walls and the bearings are well lubricated during the crank rotations. The rings around the pistons are responsible for keeping the air compressed that is at the top of the piston so that the air does not come in contact with the lubricating oil. Unfortunately, sometimes a little oil might enter the compressed air. This is why air compressors require regular check-ups, especially in cases where the tools require oil-free air.
Another new air compressor model in the market comprises a one-piece piston or connecting rod. As there is no wrist pin, the piston has to move side to side while the shaft moves it up and down. The piston has a seal around it to prevent air leakage and maintain contact with the cylinder walls at the same time.
Here are a few tips to avoid any wastage of energy in the form of leakage or unused compressed air:
-
Examine your usage levels.
-
Look for leaks and eliminate them immediately.
-
Reduce pressure drops.
-
Verify the CFM output.
-
Recover wasted heat.
-
Use flow controllers.
-
Change air filters regularly.
Air Compressors Then & Now
Until a few decades ago, most shops used a central power source to drive their tools using a system of belts, drive shafts and wheels. The power was routed all around the workspace using mechanical means. Over time, belts and shafts have disappeared, but a mechanical system is still in place to help power move around the shop. This system uses the energy stored in pressurized air by installing an air compressor. Experts from https://www.ablesales.com.au/air-compressors-factory-direct/ mention that the Air compressors are used in a wide range of situations ranging from gas stations to large manufacturing plants. In fact, air compressors have even found their way to home basements, garages, and workshops.
Picking Out A New Air Compressor
If you are looking for a new compressor for your business of home requirements, you have come to the right place. Here are a few key factors you need to remember while choosing an air compressor:
-
Size: Air compressors come in various sizes. You need to determine one that fits your requirements. Investing in a small one can be a waste of time if you run a large enterprise. You also cannot make the mistake of picking a large one and wasting precious resources.
-
Work environment: Understanding the work environment is key is deciding on an electric motor or a gasoline motor. While gasoline motors offer more portability, electric motors are less expensive and also require less maintenance.
-
Airflow: The airflow offered by an air compressor is measured in cubic feet per minute or CFM. According to the experts in the industry, the CFM output of an air compressor needs to be more than the operational CFM requirement and it also needs to be less than the maximum CFM output at the same time.
-
Size of the compressor tank: A small tank is sufficient for short, concentrated bursts of power. If you require sustained power over longer periods, you will need to invest in an air compressor that comes with a larger tank.
-
Control systems: If you do not require continuous air, a start and stop system will work perfectly fine. However, if you require speed control, you will need to use a dual control system that comes with an auxiliary valve.
-
Horsepower: The horsepower will help you determine whether the air compressor can produce enough air for your requirements.
-
External Features: An air compressor requires protection from water and extreme temperature to continue working. Experts advise choosing a compressor that comes with cast-iron construction so that it has added durability and reliability.
-
Price: Rather than investing in inexpensive air compressors and replacing them regularly, look for a unit that will last through its expected service life. Even beginners can learn how to use an air compressor in no time at all. The first thing you need to do is to check the pump oil level. If it is empty, you need to fill it till the indicated level. Then you will need to connect the hose to the regulator valve, followed by connecting your power tool to the hose. Once you are sure the attachments are in place, you need to plug in the compressor and start using it. It is a good idea to avoid using extension cords as they might cause the air compressor to start heating up.
At the end of the day, an air compressor is a useful device to have at your home, workspace as well as at large manufacturing spaces.